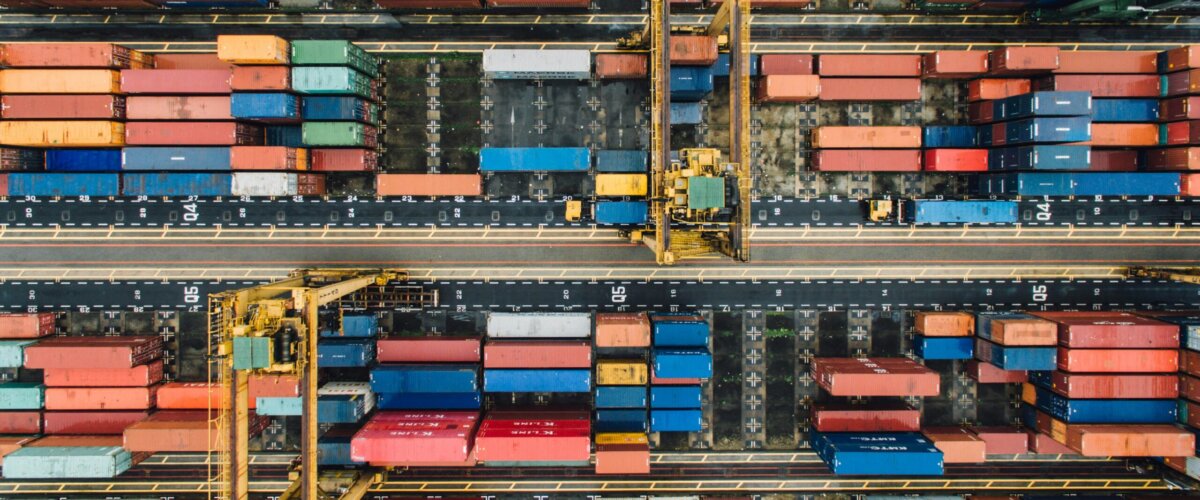
The Basic of ISO 9001
The primary purpose of ISO 9001 is to provide a standardized framework for quality management systems (QMS). It aims to help organizations consistently deliver products and services that meet customer and regulatory requirements.
Introduction
International Recognition:
ISO 9001 is introduced as an internationally recognized standard developed by the International Organization for Standardization (ISO). This global recognition emphasizes the applicability and relevance of ISO 9001 across diverse industries and geographical locations.
Importance of Quality Management:
The introduction highlights the significance of effective quality management in achieving organizational success. ISO 9001 is positioned as a tool that organizations can use to enhance their internal processes, improve customer satisfaction, and remain competitive in the marketplace.
Customer Focus:
Customer focus is emphasized as a core principle within ISO 9001. The standard encourages organizations to understand and meet customer needs, thereby enhancing customer satisfaction. This customer-centric approach is integral to the overall philosophy of ISO 9001.
Scope of the Standard:
The introduction provides a brief overview of the scope of ISO 9001, indicating that it is applicable to any organization, regardless of its size, industry, or sector. This inclusivity reinforces the versatility and broad applicability of the standard.
Compatibility with Other Standards:
ISO 9001 is introduced as part of the ISO 9000 family of standards, and the introduction may mention its compatibility with other management system standards. This compatibility allows organizations to integrate their quality management system with other management systems, such as ISO 14001 (environmental management) and ISO 45001 (occupational health and safety).
Continuous Improvement:
The concept of continuous improvement is often highlighted in the introduction. ISO 9001 encourages organizations to continually enhance their processes, products, and services, fostering a culture of ongoing improvement and adaptation to changing circumstances.
Adoption and Certification:
The introduction may touch upon the widespread adoption of ISO 9001 by organizations globally. Many organizations seek ISO 9001 certification as a way to demonstrate conformity to the standard and showcase their commitment to quality to customers, stakeholders, and regulatory bodies.
In summary, the introduction to ISO 9001 serves as a preamble to the standard, providing context on its purpose, international recognition, and the principles that guide its implementation. It sets the tone for the subsequent sections that delve into the details of the standard and its requirements.
The history of ISO 9001
ISO 9001 dates back to the mid-20th century, and its development is closely tied to the growth of quality management practices in manufacturing industries. Here’s an overview of the key milestones in the history of ISO 9001:
Post-World War II Quality Management:
In the aftermath of World War II, there was a growing recognition of the importance of quality management in manufacturing. Industries, particularly in Japan, started focusing on improving processes to ensure product quality.
Birth of Quality Management Standards:
The concept of standardized quality management systems emerged in the 1950s and 1960s. Organizations began to adopt various national standards and specifications to ensure consistency and quality in their products.
British Standard BS 5750:
The British Standards Institution (BSI) introduced the BS 5750 standard in 1979, outlining requirements for quality management systems. This standard gained popularity and was widely adopted in various industries.
Formation of ISO Technical Committee 176:
The International Organization for Standardization (ISO) established Technical Committee 176 (TC 176) in 1979, specifically focused on developing standards for quality management and quality assurance.
ISO 9000 Series Development:
Building upon the success of BS 5750, TC 176 developed the ISO 9000 series of standards, with the first version, ISO 9001, being published in 1987. This series aimed to provide a common framework for quality management systems worldwide.
Revisions and Updates:
Over the years, ISO 9001 underwent several revisions to address changing business environments and improve its relevance. Key revisions include ISO 9001:1994, ISO 9001:2000, ISO 9001:2008, and the latest major revision, ISO 9001:2015.
ISO 9001:2015 – A Shift to Risk-Based Thinking:
The 2015 revision marked a significant shift in the approach to quality management. It introduced a risk-based thinking perspective, emphasizing the identification and mitigation of risks to achieve better outcomes.
Global Adoption and Certification:
ISO 9001 gained widespread international acceptance, becoming a benchmark for quality management. Organizations across various industries sought ISO 9001 certification to demonstrate their commitment to quality and gain a competitive edge in the global market.
The history of ISO 9001 reflects the evolving understanding of quality management practices and the global standardization efforts to facilitate consistent and effective quality assurance across industries.
Integration with Other Management Systems:
ISO 9001:2015 is designed to be compatible with other ISO management system standards, allowing organizations to integrate their quality management system with environmental (ISO 14001) and occupational health and safety (ISO 45001) management systems.
The key principles of ISO 9001
The key principles reflect the fundamental concepts that guide the development and implementation of a Quality Management System (QMS). These principles are designed to help organizations enhance their processes, meet customer expectations, and continually improve their performance. Here’s an overview of the key principles of ISO 9001:
Customer Focus:
Principle: Organizations depend on their customers, and therefore they should understand current and future customer needs, meet customer requirements, and strive to exceed customer expectations.
Significance: Placing the customer at the center of the organization’s focus ensures that products and services are designed and delivered to meet customer satisfaction, fostering loyalty and positive relationships.
Leadership:
Principle: Leaders at all levels of the organization should establish unity of purpose and direction. They should create and maintain the internal environment in which people can become fully involved in achieving the organization’s objectives.
Significance: Effective leadership provides the vision, direction, and support necessary for the implementation of the QMS. It encourages a culture of quality throughout the organization.
Engagement of People:
Principle: Competent, empowered, and engaged people at all levels within the organization are essential for the achievement of organizational objectives.
Significance: Involving and empowering employees fosters a sense of ownership, responsibility, and commitment. Engaged employees contribute more effectively to the success of the QMS.
Process Approach:
Principle: A desired result is achieved more efficiently when activities and related resources are managed as a process.
Significance: Viewing the organization as a set of interconnected processes helps identify and understand how inputs are transformed into outputs. This approach enhances efficiency, effectiveness, and the ability to meet objectives.
Improvement:
Principle: Continuous improvement is a permanent objective of the organization.
Significance: Regularly assessing and improving processes, products, and the QMS itself leads to enhanced performance and increased customer satisfaction. The focus on continual improvement is integral to the ISO 9001 philosophy.
Evidence-Based Decision Making:
Principle: Decisions based on the analysis and evaluation of data and information are more likely to produce desired results.
Significance: Using data-driven decision-making ensures that decisions are well-informed and align with the organization’s objectives. It promotes objectivity and reduces reliance on assumptions.
Relationship Management:
Principle: An organization and its external providers are interdependent and a mutually beneficial relationship enhances the ability to create value.
Significance: Building positive relationships with suppliers and other external partners is crucial for the success of the organization. Collaboration and effective communication contribute to shared success.
These key principles collectively form the foundation of ISO 9001 and provide a holistic approach to quality management. Organizations that integrate these principles into their operations are better equipped to establish, implement, and continually improve their QMS, leading to sustained success and customer satisfaction.
The benefits of implementing ISO 9001
The benefits of implementing ISO 9001 are extensive and can positively impact organizations across various industries. Here’s an overview of the key benefits associated with ISO 9001:
Increased Efficiency:
ISO 9001 emphasizes a process-oriented approach to quality management. By identifying, documenting, and optimizing key processes, organizations can enhance efficiency, reduce waste, and streamline their operations.
Improved efficiency often leads to cost savings, quicker response times, and a more agile and adaptable organization.
Enhanced Customer Satisfaction:
ISO 9001 places a strong emphasis on meeting customer requirements and expectations. By implementing a QMS, organizations can better understand customer needs, deliver consistent and high-quality products or services, and improve overall customer satisfaction.
Satisfied customers are more likely to be loyal, provide positive feedback, and contribute to the organization’s reputation and success.
Improved Market Competitiveness:
ISO 9001 certification is widely recognized and often considered a benchmark for quality. Achieving and maintaining certification can enhance an organization’s credibility, making it more competitive in the marketplace.
ISO 9001 certification can open up new business opportunities, attract customers who prioritize quality, and provide a competitive edge over non-certified competitors.
Regulatory Compliance:
ISO 9001 provides a framework for organizations to comply with relevant regulatory requirements and standards. It helps ensure that products and services meet legal and regulatory specifications.
Compliance reduces the risk of legal issues, fines, and other penalties, instilling confidence in stakeholders and demonstrating a commitment to ethical business practices.
Systematic Approach to Management:
ISO 9001 encourages a systematic and structured approach to management. The standard defines clear roles, responsibilities, and processes, fostering a well-organized and efficient working environment.
A systematic approach improves decision-making, reduces ambiguity, and facilitates better communication and collaboration within the organization.
Facilitates Continuous Improvement:
ISO 9001 promotes a culture of continuous improvement. Organizations are encouraged to regularly assess their processes, gather data, and identify opportunities for enhancement.
Continuous improvement leads to ongoing optimization of processes, products, and services, ensuring that the organization remains competitive and adaptable to changing circumstances.
Risk Management:
ISO 9001:2015 introduced a stronger emphasis on risk-based thinking. Organizations are required to identify and manage risks to the achievement of their objectives.
Proactive risk management helps organizations anticipate and address potential issues, minimizing the likelihood of disruptions and enhancing overall resilience.
Employee Engagement and Satisfaction:
ISO 9001 emphasizes the importance of engaging employees in the quality management process. Involving employees in decision-making and improvement initiatives contributes to job satisfaction and a positive workplace culture.
Engaged and satisfied employees are more likely to contribute to the success of the QMS, leading to improved overall performance.
International Recognition:
ISO 9001 is recognized and respected globally. Achieving certification demonstrates an organization’s commitment to quality on an international scale.
International recognition can be especially beneficial for organizations involved in global trade, as it facilitates easier entry into new markets and builds trust with international stakeholders.
Customer Trust and Confidence:
ISO 9001 certification enhances customer trust and confidence. It provides assurance that an organization has implemented effective quality management practices and is committed to delivering quality products or services.
Building trust with customers is essential for long-term relationships, repeat business, and positive word-of-mouth referrals.
In summary, the benefits of ISO 9001 extend across operational, financial, and reputational aspects of an organization. Implementing a QMS based on ISO 9001 principles can lead to sustained improvements, increased customer satisfaction, and a competitive advantage in the marketplace.
Implementing ISO 9001
Implementing ISO 9001 involves a structured process to establish, document, and maintain a Quality Management System (QMS) that aligns with the requirements of the standard. The implementation process is crucial for organizations seeking ISO 9001 certification or aiming to improve their overall quality management practices. Here’s an overview of the implementation process for ISO 9001:
Leadership Commitment:
Top management plays a crucial role in leading and supporting the implementation of ISO 9001. Leadership commitment involves understanding the benefits of the QMS, allocating resources, and actively promoting a culture of quality within the organization.
Express commitment through a formal quality policy, allocate necessary resources, and communicate the importance of ISO 9001 implementation.
Utilizing a Risk-Based Approach:
ISO 9001:2015 introduced a stronger emphasis on risk-based thinking. Organizations need to identify and assess risks and opportunities that could affect the achievement of their objectives.
Conduct a risk assessment to identify potential risks and opportunities. Develop plans to address and mitigate identified risks while leveraging opportunities for improvement.
Engaging Employees in the Process:
Employee involvement is essential for the success of the QMS. Engaged employees are more likely to contribute to the identification of improvement opportunities and adherence to quality processes.
Provide training on ISO 9001 principles, involve employees in decision-making, and encourage a culture of continuous improvement. Communicate the benefits of ISO 9001 to build enthusiasm and commitment.
Step-by-Step Guide to Implementation:
Develop a systematic plan for implementing the QMS. This plan should include specific steps to follow, deadlines, and assigned responsibilities.
Create a project team responsible for implementation. Develop a detailed implementation plan, including a timeline, tasks, and responsible parties. Ensure that everyone involved understands their roles and responsibilities.
Documenting the QMS:
Documentation is a key component of ISO 9001. Organizations need to document their processes, policies, and procedures to ensure consistency and traceability.
Create documentation that outlines the QMS, including a quality manual, procedures, work instructions, and forms. Ensure that documentation is accessible and understood by relevant personnel.
Training and Awareness:
Ensure that employees at all levels are adequately trained and aware of the requirements and expectations of ISO 9001.
Provide training sessions on the QMS, including the principles of ISO 9001, specific procedures, and any changes to existing processes. Raise awareness of the importance of individual contributions to the QMS.
Internal Audits:
Internal audits are a crucial part of the implementation process. They help organizations assess the effectiveness of their QMS and identify areas for improvement.
Conduct regular internal audits to evaluate conformity to ISO 9001 requirements. Use audit findings to make improvements to the QMS.
Management Review:
Management review involves top management periodically assessing the QMS to ensure its continued suitability, adequacy, and effectiveness.
Schedule and conduct management review meetings to evaluate the QMS’s performance. Review data on customer feedback, audit results, and other relevant information. Make decisions on improvements and updates to the QMS.
Certification Process:
Organizations seeking ISO 9001 certification can undergo an external audit by a certification body. This process involves a comprehensive evaluation of the QMS to ensure compliance with ISO 9001 requirements.
Choose a reputable certification body and undergo a certification audit. Address any non-conformities identified during the audit. Once compliance is confirmed, the organization receives ISO 9001 certification.
Continuous Improvement:
ISO 9001 is built on the principle of continuous improvement. Organizations must continually assess their processes, seek feedback, and implement corrective actions to enhance the QMS.
Establish a culture of continuous improvement. Encourage feedback from employees and stakeholders. Regularly assess processes and performance data to identify areas for enhancement.
By following these steps, organizations can successfully implement ISO 9001, fostering a culture of quality, improving operational efficiency, and enhancing overall customer satisfaction. The implementation process is not a one-time effort but a continuous journey toward excellence and improvement.