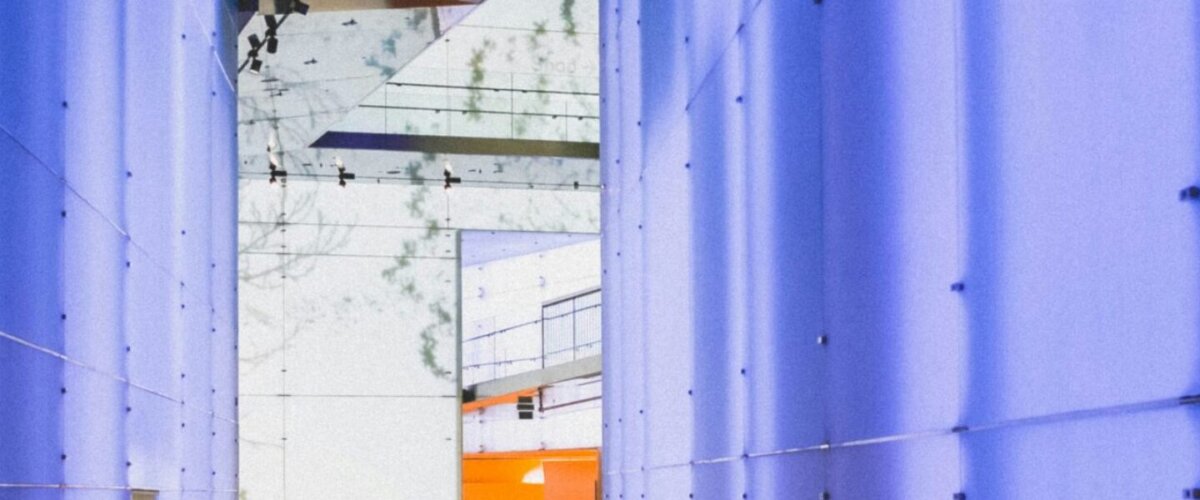
IATF 16949 – Quality in the Automotive Industry
IATF 16949 is a globally recognized quality management standard developed by the International Automotive Task Force (IATF), a consortium comprising automotive manufacturers and their respective trade associations. It builds upon the principles of ISO 9001 while incorporating automotive-specific requirements to enhance product quality, efficiency, and customer satisfaction.
What is Quality Management according to IATF 16949?
The global automotive industry stands for excellent process quality, continuous improvement processes, the highest standards, and innovation. IATF 16949 is the standard for quality management systems for suppliers in the automotive industry.
The standard was developed by a joint working group, the International Automotive Task Force IATF, with the aim of improving quality capacity and the entire certification process within the supply chain – to ensure system and process quality to the highest degree. Since its publication in October 2016, IATF 16949 has succeeded ISO/TS 16949, thus becoming the entry ticket for this internationally active industry.
IATF 16949 follows the ISO’s common structure for management system standards (High Level Structure) and complements the globally recognized ISO 9001:2015 standard with the expanded industry requirements. As a result of the review, the standard has undergone several automotive-specific changes in addition to the adaptation to ISO 9001, such as managing safety-relevant parts, for products with integrated software, and for traceability.
What are the benefits of IATF 16949 certification?
Most OEM* members of IATF require mandatory evidence of a quality management system. Whether it’s a small company, a medium-sized company, or a corporate group, an IATF 16949 certificate is their ticket to enter the automotive industry. * OEM Original Equipment Manufacturer
Companies certified according to IATF 16949 improve the reliability and process capability of the entire supply chain, minimize defects and risks, and help reduce waste throughout the supply chain. Therefore, the IATF 16949 standard is relevant in terms of customer-specific requirements for anyone working for the automotive industry in production or assembly, or listed as potential external suppliers.
Why is an IATF 16949 certificate useful for your company?
Independent and expert certification of the management system provides top management with assurance that the system meets the requirements of IATF 16949. With its holistic view of people, processes, and results, our auditors identify improvement potential and provide guidance for decision-making processes. By continuously optimizing processes and continuous improvement of your organization, you improve your performance level, minimize losses, and deliver the highest process quality for your company.
What is IATF?
The working group was founded in 1996 and today represents all major OEM manufacturers (original equipment manufacturers) and national supplier organizations in the USA, India, and Europe (Germany, France, the United Kingdom, and Italy). However, not all international car manufacturers are members of IATF, especially not in Southeast Asia (Japan, South Korea, and China, for example). With one exception: the Geely group, which includes Volvo among others.
IATF’s mission is to harmonize nationally implemented quality management methods and quality management standards to improve the overall product quality in the automotive industry. IATF is also the publisher of the technical standard IATF 16949, which sets requirements for a quality management system for series and spare parts production in the automotive industry. In 2016, IATF 16949 followed the technical specification ISO/TS 16949, which was first published in 1999 with the participation of the International Organization for Standardization (ISO). In addition, there are the so-called “rules,” which contain requirements for certification bodies accredited to perform certification audits according to IATF 16949. The actual target group for IATF’s quality requirements is primarily the group of international and national automotive suppliers, mostly so-called “tier 1 suppliers” and “tier 2 suppliers.” Car manufacturers generally require evidence of their quality capability from them in the form of an IATF 16949 certificate. Expertise and Trust The technical specification ISO/TS 16949 was first published in March 1999. The aim was to harmonize the quality requirements of the automotive industry, which had varied internationally until then. In 2000, DQS was recognized as a certifier by IATF and approved by the German VDA-QMC (Quality Management Center of the German Automotive Industry Association). Since then, we have been one of the most experienced certification companies for automotive standards worldwide.
CARA – Common Application of Audit Reports
IATF has developed a tool for audit documentation called “CARA – Common Audit Report Application.” The main purpose is to harmonize audit documentation, which was previously handled individually by certification bodies. In the future, audit documents will be created, edited, stored, and used in a standardized manner. In the future, all IATF auditors worldwide will document audit results on a common platform, regardless of which certification body they work for. CARA is an IATF browser-based application that does not require any additional software to be installed in your organization. The application is also not linked to a server or a cloud. All audit data created and imported is stored only in the internal database of each user’s browser, which can be accessed offline (without an internet connection). This, in turn, requires the user to work with this single browser only, as no access is possible from other browsers. The use of the tool is mandatory for all IATF audit procedures from January 1, 2021.
Core Tools
The Core Tools outlined in IATF 16949 serve as essential instruments for achieving and maintaining automotive quality standards. They provide structured methodologies for various aspects of quality management, including product development, manufacturing processes, and problem-solving. Let’s delve into each:
- Advanced Product Quality Planning (APQP): APQP is a structured approach to product development and launch within the automotive industry. It involves cross-functional teamwork to define and document product and process requirements, establish validation criteria, and mitigate risks throughout the development cycle. APQP ensures that products meet customer expectations while adhering to regulatory requirements.
- Production Part Approval Process (PPAP): PPAP is a standardized process for demonstrating that production processes are capable of consistently manufacturing products that meet specified requirements. Suppliers submit PPAP documents to automotive manufacturers, providing evidence of part conformance, process capability, and product quality. PPAP helps ensure that suppliers can reliably meet customer expectations and regulatory requirements.
- Failure Mode and Effects Analysis (FMEA): FMEA is a proactive risk assessment tool used to identify and prioritize potential failure modes within a product or process. By systematically analyzing failure modes, their causes, and their effects, organizations can implement preventive measures to minimize risks and improve product reliability. FMEA fosters a culture of continuous improvement and risk mitigation across the supply chain.
- Measurement System Analysis (MSA): MSA evaluates the reliability and accuracy of measurement systems used in production processes. It assesses various factors, such as equipment calibration, operator proficiency, and environmental conditions, to ensure that measurement data is trustworthy and consistent. MSA helps organizations make informed decisions based on reliable data, ultimately enhancing product quality and process efficiency.
- Statistical Process Control (SPC): SPC is a methodology for monitoring and controlling manufacturing processes to ensure they operate within specified limits and produce consistent output. By collecting and analyzing process data in real-time, SPC enables organizations to detect and address variations, identify trends, and prevent defects before they occur. SPC empowers organizations to achieve higher levels of process stability and product quality.
- Control Plan: The control plan is a documented strategy that outlines how key process characteristics will be monitored, controlled, and improved to meet customer requirements. It identifies process controls, inspection activities, and response plans for managing deviations and non-conformities. Control plans serve as living documents that guide process management and continuous improvement efforts.