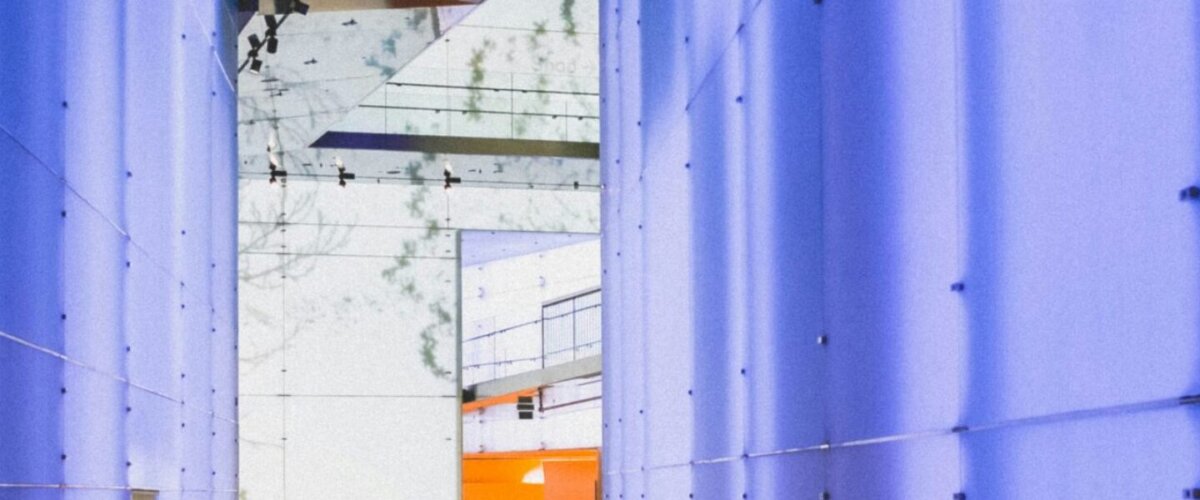
IATF 16949 – Qualität in der Automobilbranche
Die IATF 16949 ist eine weltweit anerkannte Qualitätsmanagementnorm, die von der International Automotive Task Force (IATF), einem Konsortium aus Automobilherstellern und ihren jeweiligen Fachverbänden, entwickelt wurde. Sie baut auf den Grundsätzen der ISO 9001 auf und enthält gleichzeitig automobilspezifische Anforderungen zur Verbesserung von Produktqualität, Effizienz und Kundenzufriedenheit.
Was ist Qualitätsmanagement nach IATF 16949?
Die weltweite Automobilindustrie steht für exzellente Prozessqualität, kontinuierliche Verbesserungsprozesse, höchste Standards und Innovation. Die IATF 16949 ist der Standard für Qualitätsmanagementsysteme für Zulieferer in der Automobilindustrie.
Der Standard wurde von einer gemeinsamen Arbeitsgruppe, der International Automotive Task Force IATF, mit dem Ziel entwickelt, die Qualitätsfähigkeit und den gesamten Zertifizierungsprozess innerhalb der Lieferkette zu verbessern – um System- und Prozessqualität auf höchstem Niveau sicherzustellen. Seit ihrer Veröffentlichung im Oktober 2016 hat die IATF 16949 die ISO/TS 16949 abgelöst und ist damit die Eintrittskarte für diese international tätige Branche.
Die IATF 16949 folgt der gemeinsamen Struktur der ISO für Managementsystemnormen (High Level Structure) und ergänzt die weltweit anerkannte Norm ISO 9001:2015 um die erweiterten Branchenanforderungen. Als Ergebnis der Überarbeitung hat die Norm neben der Anpassung an die ISO 9001 mehrere automobilspezifische Änderungen erfahren, wie z.B. für das Management sicherheitsrelevanter Teile, für Produkte mit integrierter Software und für die Rückverfolgbarkeit.
Was sind die Vorteile einer IATF 16949-Zertifizierung?
Die meisten OEM*-Mitglieder der IATF verlangen zwingend den Nachweis eines Qualitätsmanagementsystems. Ob es sich um ein kleines Unternehmen, ein mittelständisches Unternehmen oder einen Konzern handelt, ein IATF 16949-Zertifikat ist ihre Eintrittskarte in die Automobilindustrie. * OEM Original Equipment Manufacturer
Nach IATF 16949 zertifizierte Unternehmen verbessern die Zuverlässigkeit und Prozessfähigkeit der gesamten Lieferkette, minimieren Fehler und Risiken und helfen, Verschwendung in der gesamten Lieferkette zu reduzieren. Daher ist die IATF 16949-Norm im Hinblick auf die kundenspezifischen Anforderungen für jeden relevant, der für die Automobilindustrie in der Produktion oder Montage arbeitet oder als potenzieller externer Lieferant gelistet ist.
Warum ist ein IATF 16949-Zertifikat für Ihr Unternehmen sinnvoll?
Die unabhängige und fachkundige Zertifizierung des Managementsystems gibt der Unternehmensleitung die Sicherheit, dass das System die Anforderungen der IATF 16949 erfüllt. Durch die ganzheitliche Betrachtung von Menschen, Prozessen und Ergebnissen zeigen unsere Auditoren Verbesserungspotenziale auf und geben Hilfestellung bei Entscheidungsprozessen. Durch die kontinuierliche Optimierung von Prozessen und die ständige Verbesserung Ihrer Organisation steigern Sie Ihr Leistungsniveau, minimieren Verluste und sorgen für höchste Prozessqualität in Ihrem Unternehmen.
Was ist die IATF?
Die Arbeitsgruppe wurde 1996 gegründet und vertritt heute alle großen OEM-Hersteller (Original Equipment Manufacturer) und nationalen Zulieferorganisationen in den USA, Indien und Europa (Deutschland, Frankreich, Großbritannien und Italien). Allerdings sind nicht alle internationalen Automobilhersteller Mitglieder der IATF, insbesondere nicht in Südostasien (z. B. Japan, Südkorea und China). Mit einer Ausnahme: der Geely-Gruppe, zu der unter anderem Volvo gehört.
Die Aufgabe der IATF besteht darin, die auf nationaler Ebene eingeführten Qualitätsmanagementmethoden und -normen zu harmonisieren, um die allgemeine Produktqualität in der Automobilindustrie zu verbessern. Die IATF ist auch der Herausgeber der technischen Norm IATF 16949, die Anforderungen an ein Qualitätsmanagementsystem für die Serien- und Ersatzteilproduktion in der Automobilindustrie festlegt. Im Jahr 2016 folgte die IATF 16949 der technischen Spezifikation ISO/TS 16949, die erstmals 1999 unter Beteiligung der Internationalen Organisation für Normung (ISO) veröffentlicht wurde. Hinzu kommen die sogenannten „Rules“, die Anforderungen an Zertifizierungsstellen enthalten, die akkreditiert sind, Zertifizierungsaudits nach IATF 16949 durchzuführen. Die eigentliche Zielgruppe für die Qualitätsanforderungen der IATF ist in erster Linie die Gruppe der internationalen und nationalen Automobilzulieferer, meist so genannte „Tier 1 Supplier“ und „Tier 2 Supplier“. Von ihnen verlangen die Automobilhersteller in der Regel den Nachweis ihrer Qualitätsfähigkeit in Form eines IATF 16949-Zertifikats. Kompetenz und Vertrauen Die technische Spezifikation ISO/TS 16949 wurde erstmals im März 1999 veröffentlicht. Ziel war es, die bis dahin international unterschiedlichen Qualitätsanforderungen der Automobilindustrie zu harmonisieren. Im Jahr 2000 wurde die DQS von der IATF als Zertifizierer anerkannt und vom deutschen VDA-QMC (Qualitätsmanagement-Center des Verbandes der Automobilindustrie) zugelassen. Seitdem sind wir eine der erfahrensten Zertifizierungsgesellschaften für Automobilstandards weltweit.
CARA – Gemeinsame Anwendung von Auditberichten
Die IATF hat ein Instrument zur Auditdokumentation entwickelt, das CARA – Common Audit Report Application“ genannt wird. Das Hauptziel ist die Harmonisierung der Auditdokumentation, die bisher von den Zertifizierungsstellen individuell gehandhabt wurde. Künftig sollen Auditdokumente einheitlich erstellt, bearbeitet, gespeichert und verwendet werden. Künftig werden alle IATF-Auditoren weltweit Auditergebnisse auf einer gemeinsamen Plattform dokumentieren, unabhängig davon, für welche Zertifizierungsstelle sie arbeiten. CARA ist eine browserbasierte IATF-Anwendung, für die keine zusätzliche Software in Ihrem Unternehmen installiert werden muss. Die Anwendung ist auch nicht mit einem Server oder einer Cloud verbunden. Alle erstellten und importierten Auditdaten werden nur in der internen Datenbank des Browsers des jeweiligen Benutzers gespeichert, auf die offline (ohne Internetverbindung) zugegriffen werden kann. Dies wiederum setzt voraus, dass der Nutzer nur mit diesem einen Browser arbeitet, da kein Zugriff von anderen Browsern aus möglich ist. Die Verwendung des Tools ist für alle IATF-Auditverfahren ab dem 1. Januar 2021 obligatorisch.
Kern-Tools
Die in der IATF 16949 beschriebenen Core Tools dienen als wesentliche Instrumente zur Erreichung und Aufrechterhaltung von Qualitätsstandards in der Automobilindustrie. Sie bieten strukturierte Methoden für verschiedene Aspekte des Qualitätsmanagements, einschließlich Produktentwicklung, Fertigungsprozesse und Problemlösung. Schauen wir uns die einzelnen Punkte an:
- Erweiterte Produktqualitätsplanung (APQP): APQP ist ein strukturierter Ansatz für die Produktentwicklung und -einführung in der Automobilbranche. Es beinhaltet funktionsübergreifende Teamarbeit, um Produkt- und Prozessanforderungen zu definieren und zu dokumentieren, Validierungskriterien festzulegen und Risiken während des gesamten Entwicklungszyklus zu minimieren. APQP stellt sicher, dass die Produkte die Kundenerwartungen erfüllen und gleichzeitig die gesetzlichen Vorschriften einhalten.
- Produktionsteil-Freigabeverfahren (PPAP): PPAP ist ein standardisiertes Verfahren, mit dem nachgewiesen wird, dass die Produktionsprozesse in der Lage sind, Produkte zu fertigen, die den festgelegten Anforderungen entsprechen. Die Zulieferer reichen PPAP-Dokumente bei den Automobilherstellern ein und weisen damit die Konformität der Teile, die Prozessfähigkeit und die Produktqualität nach. PPAP trägt dazu bei, dass die Zulieferer die Kundenerwartungen und gesetzlichen Anforderungen zuverlässig erfüllen können.
- Fehlermöglichkeits- und -einflussanalyse (FMEA): Die FMEA ist ein proaktives Risikobewertungsinstrument zur Identifizierung und Priorisierung potenzieller Fehlermöglichkeiten innerhalb eines Produkts oder Prozesses. Durch die systematische Analyse von Fehlermöglichkeiten, deren Ursachen und Auswirkungen können Unternehmen vorbeugende Maßnahmen zur Risikominimierung und Verbesserung der Produktzuverlässigkeit ergreifen. Die FMEA fördert eine Kultur der kontinuierlichen Verbesserung und Risikominderung in der gesamten Lieferkette.
- Messsystemanalyse (MSA): Die MSA bewertet die Zuverlässigkeit und Genauigkeit von Messsystemen, die in Produktionsprozessen eingesetzt werden. Dabei werden verschiedene Faktoren wie die Kalibrierung der Geräte, die Fähigkeiten der Bediener und die Umgebungsbedingungen bewertet, um sicherzustellen, dass die Messdaten vertrauenswürdig und konsistent sind. MSA hilft Unternehmen, fundierte Entscheidungen auf der Grundlage zuverlässiger Daten zu treffen und so die Produktqualität und Prozesseffizienz zu verbessern.
- Statistische Prozesskontrolle (SPC): SPC ist eine Methode zur Überwachung und Steuerung von Fertigungsprozessen, um sicherzustellen, dass diese innerhalb bestimmter Grenzen ablaufen und eine gleichbleibende Leistung erbringen. Durch die Erfassung und Analyse von Prozessdaten in Echtzeit ermöglicht SPC Unternehmen, Abweichungen zu erkennen und zu beheben, Trends zu erkennen und Fehler zu vermeiden, bevor sie auftreten. SPC versetzt Unternehmen in die Lage, ein höheres Maß an Prozessstabilität und Produktqualität zu erreichen.
- Kontrollplan: Der Kontrollplan ist eine dokumentierte Strategie, die darlegt, wie die wichtigsten Prozessmerkmale überwacht, gesteuert und verbessert werden, um die Kundenanforderungen zu erfüllen. Er identifiziert Prozesskontrollen, Inspektionsaktivitäten und Reaktionspläne für den Umgang mit Abweichungen und Nichtkonformitäten. Kontrollpläne dienen als lebende Dokumente, die das Prozessmanagement und die kontinuierlichen Verbesserungsbemühungen anleiten.